Design Essentials for Hot-Fill PET Preforms
Discover the critical design factors for PET preforms in hot-fill applications. Learn how an industrial polymers company helps optimize performance under high temperatures.
Fruit juices, isotonic drinks, flavored waters, sauces, and other food items that need to be sterilized at high temperatures must be packaged in hot-fill containers. Hot-filling requires packaging that can tolerate high temperatures—typically up to 85–95°C—without sacrificing structural integrity or product safety, in contrast to conventional cold-fill procedures. Because of its ability to balance strength, clarity, and recyclability, PET (polyethylene terephthalate) has emerged as the preferred material for these kinds of applications. However, the preform design has a significant impact on a hot-fill PET bottle's success.
It takes precise science to create PET preforms that work well in hot-fill situations. Process engineers, materials scientists, and frequently an experienced industrial polymers company that specializes in innovative polymer formulations must work closely together. The main elements that affect the design of PET preforms for hot-fill applications are examined here.
Understanding Heat-Set Technology
Heat-set technology is the cornerstone of each PET bottle that is ready for hot filling. Hot-fill bottles are manufactured using a controlled heat-setting technique, in contrast to traditional PET containers that are blow-molded and instantly cooled. By increasing the PET's crystallinity, this method allows it to withstand higher temperatures without deforming.
The preform is heated during blow molding and then expanded inside a hot mold, which is normally maintained at a temperature of 120 to 180°C. The PET's molecular chains can reorganize into a more stable crystalline structure by keeping the bottle in this mold for a predetermined amount of time. The preform's composition and design are much more crucial because the degree of crystallinity attained directly impacts the container's heat resistance.
Material Selection for Thermal Resistance
When creating preforms for hot-fill applications, selecting the appropriate resin formulation is essential. The necessary dimensional stability and heat resistance may not be provided by standard PET grades. Therefore, to encourage quicker and more consistent crystallization during the heat-set process, materials strengthened with nucleating agents or copolyesters are frequently utilized.
Specialty PET resins made especially for hot-fill settings are available from an industrial polymers company. These resins might contain additives that increase mold release, preform processability, and thermal performance. By choosing the best resin, the finished bottle will keep its form during hot filling and for the duration of its shelf life.
Wall Thickness and Uniformity
The thickness and consistency of the preform walls are additional crucial design considerations. Warping or paneling, in which portions of the bottle collapse inward as a result of a vacuum formed during cooling, might result from uneven material distribution. In hot-fill applications, where internal pressures fluctuate quickly, this is particularly problematic.
In order to solve this, preform designers concentrate on improving the shape to permit consistent wall stretching during blow molding and establishing even material flow during injection molding. This makes it possible to guarantee that crucial sections—like the base, sidewalls, and shoulder—have enough thickness to withstand deformation. To improve strength and stability, the base of the bottle may occasionally be shaped like a petaloid.
Neck Finish and Dimensional Control
Although they are frequently disregarded, neck finishes are an essential part of hot-fill packing. During hot-filling, the neck region must stay sufficiently rigid to sustain closures and sealing without undergoing distortion. To maintain dimensional precision, the neck is therefore usually maintained in an amorphous form, avoiding crystallization.
Tight tolerances and uniformity in the neck dimensions between batches must be guaranteed by the manufacturers. By doing this, problems with capping or leaks during distribution are avoided. Long-term packing performance can be ensured by a precise injection molding technique, which is frequently made possible by mold designs created in collaboration with an industrial polymers company.
Vacuum Compensation Features
The bottle is sealed and allowed to cool after being hot-filled. A vacuum is created inside the bottle as the liquid cools. This may cause the container to collapse if left unchecked. Vacuum panels or flexible sections that absorb the pressure differential without changing the overall form are used in PET bottle designs to combat this.
These characteristics need to be taken into account during the preform design phase. In order to guarantee that the blown container has enough material in panel areas and the mechanical flexibility needed to withstand vacuum forces, proper preform shape is essential. This method enhances both practical and visual performance because vacuum panels can be used as branding or grip zones.
Transparency and Aesthetic Requirements
PET's aesthetic appeal is a primary factor in manufacturers' decision to use it for hot-fill items rather than glass. For juice, tea, and other beverages where color and texture influence perceived freshness and quality, PET's exceptional clarity enables customers can see the product within.
It's not always easy to get this transparency in a heat-set bottle, though. Color changes or haze are frequently caused by higher crystallinity. Preform design must strike a balance between optical clarity and thermal stability in order to lessen this. An industrial polymers company's advanced resin compositions can assist in striking this balance by providing better crystallization without sacrificing transparency.
Sustainability and Lightweighting Considerations
Sustainability is still a top concern, even though handling heat and vacuum requires more material. Lightweighting techniques are used in modern PET preform design to minimize resin usage without sacrificing performance. These include precisely developed preform forms that remove extra material in non-load-bearing areas, enhanced stretching ratios during blow molding, and optimized bottle profiles.
Additionally, producers can now employ more environmentally friendly materials without compromising hot-fill performance thanks to advancements in bio-based PET and post-consumer recycled (PCR) PET. As businesses work to achieve environmental goals, it is becoming more and more vital to design preforms to handle various types of resin.
Manufacturing Precision and Quality Control
Creating the perfect preform is just one aspect of the problem. In large production, execution is equally important. Real-time monitoring of critical parameters including preform temperature, injection pressure, and cooling time, as well as equipment calibration and mold maintenance, are all crucial.
Working with a reputable industrial polymers company guarantees technical assistance during the manufacturing process in addition to access to specialist resources. These businesses frequently offer data-driven insights about bottle stress spots, preform performance, and mold behavior, empowering producers to conduct proactive troubleshooting and preserve constant product quality.
Future-Ready Design Strategy
The design of PET preforms will keep changing as hot-fill products become more varied. Designs will increasingly have to take into consideration the demands of the global supply chain, shifting consumer tastes, and more stringent regulatory requirements. Future preform design will be influenced by including clever features like QR codes, tamper-evident neck bands, or enhanced recyclability.
Those who approach perform design as a dynamic innovation process rather than a static engineering effort will succeed in this quickly evolving industry. Delivering dependable, effective, and future-ready hot-fill PET packaging will require careful coordination with materials experts as well as ongoing input from filling lines and distribution channels.
What's Your Reaction?
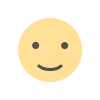

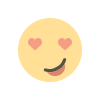


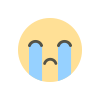
