Common Defects in Molded Pulp and How QA Can Prevent Them
One of the most common defects in molded pulp products is inconsistent thickness. Variability in material distribution can result in weak spots,
Molded pulp packaging is widely used in various industries due to its sustainability, cost-effectiveness, and biodegradability. However, like any manufacturing process, molded pulp production is prone to defects that can impact the quality, functionality, and appearance of the final product. Effective Quality Assurance (QA) is essential to minimize defects and ensure that molded pulp packaging meets industry standards. This article discusses common defects in molded pulp and how QA for molded pulp can prevent them.
Inconsistent Thickness
One of the most common defects in molded pulp products is inconsistent thickness. Variability in material distribution can result in weak spots, reducing structural integrity and leading to breakage or deformation. This defect is often caused by improper slurry consistency, uneven mold pressure, or suboptimal drying conditions. If thickness inconsistencies persist, they can compromise product durability, leading to failures during transportation or usage.
QA for molded pulp can address this defect by implementing precise control over pulp slurry composition and mold pressure. Regular monitoring of slurry viscosity and fiber distribution ensures uniformity in thickness. Additionally, calibrating molding equipment and conducting periodic inspections can help identify and correct inconsistencies before they impact large production batches.
Surface Imperfections
Surface imperfections such as rough textures, cracks, or indentations are another prevalent issue in molded pulp products. These defects can arise from several factors, including insufficient mold cleaning, improper drying temperatures, or variations in pulp composition. Such imperfections not only affect the visual appeal of the product but may also create weak points that lead to premature failure.
Implementing thorough QA for molded pulp can significantly reduce surface imperfections. Regular mold maintenance and cleaning prevent residue buildup that could transfer to finished products. Moreover, maintaining optimal drying conditions and ensuring consistent fiber blending can enhance the smoothness and integrity of the molded pulp surface.
Weak Structural Integrity
Structural weaknesses in molded pulp products can occur due to improper molding pressure, inadequate fiber bonding, or insufficient drying. Weak structures may not support intended loads, leading to customer dissatisfaction and potential product recalls. This defect is especially problematic in protective packaging, where strength is a primary concern.
A robust QA process includes conducting strength tests and load-bearing assessments to ensure structural integrity. By optimizing mold pressure settings and refining pulp formulations, manufacturers can enhance fiber bonding and produce stronger products. Routine stress testing further helps identify weaknesses before defective items reach the market.
Warping and Deformation
Warping and deformation are common defects that occur when molded pulp products are exposed to uneven drying conditions or excessive moisture during storage. These defects can lead to misshapen products that do not fit properly within packaging systems, causing functional and aesthetic issues. Warping is often exacerbated by fluctuations in humidity and temperature during the drying or curing process.
To prevent warping, QA for molded pulp should include controlled drying procedures with consistent temperature and humidity settings. Implementing proper storage conditions and using moisture-resistant coatings when necessary can further reduce the risk of deformation. Regular inspections help detect early signs of warping, allowing manufacturers to make timely adjustments.
Color Variations and Contaminations
Color variations and contaminations in molded pulp products can occur due to inconsistent raw material sources, improper pigment mixing, or contamination from residual mold debris. While slight color variations may be acceptable for some applications, significant inconsistencies can affect brand presentation and consumer perception. Additionally, contaminants such as dirt, dust, or foreign particles can compromise product safety and quality.
A stringent QA process ensures that raw materials are sourced from reliable suppliers with consistent quality. Implementing thorough cleaning protocols for molds and processing equipment can minimize contamination risks. Additionally, using precise color-matching techniques and regular quality checks can help maintain uniform color consistency across production batches.
Conclusion
Defects in molded pulp products can significantly impact their performance, durability, and overall quality. Implementing a comprehensive QA process is crucial for preventing defects such as inconsistent thickness, surface imperfections, weak structures, warping, and color variations. By maintaining strict quality controls at every stage of production, manufacturers can ensure that their molded pulp products meet industry standards and customer expectations. Effective QA for molded pulp not only enhances product reliability but also contributes to a more sustainable and efficient manufacturing process.
What's Your Reaction?
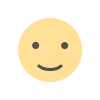

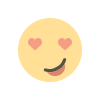


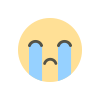
